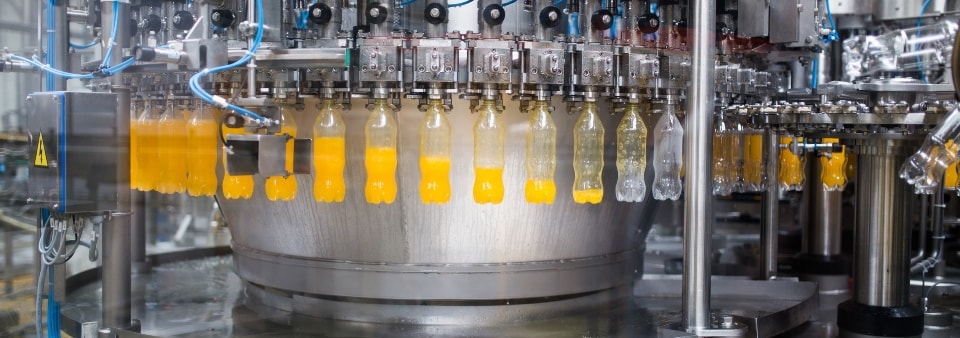
Published: August 2022
Total Productive Maintenance (TPM) was first developed as a management discipline in Japan in 1971 and was initially adopted by industries supplying the automotive sector. It’s a methodology that aims to create a corporate system that maximizes the efficiency of production systems, bringing an overall efficiency improvement. This is realized by creating systems for preventing the occurrence of all losses on the front line, including systems for realizing "zero accidents, zero defects, and zero failures" over the whole life cycle of the production system.
TPM is also applied in across the organization, including in the production, development, and administration departments. Moreover, it calls for the participation of all members, ranging from the top management to front line employees. The aim is to achieves zero losses through overlapping small-group activities.
The growth of TPM
From its beginnings in Japan, TPM quickly grew. Over the next half century word of its effectiveness spread, resulting in its much wider adoption globally and across many different industries.
This is largely beneficial. However, in some cases organizations working to adopt the TPM approach don’t get it quite right and TPM is not implemented entirely correctly. The result hurts the reputation of TPM and disappoints many who seek to benefit from its use.
BSI has now stepped in to help remedy this situation. We worked with The JIPM Corporation, co-creators of TPM, and then set up a steering group. Their work has produced PAS 1918:2022 Total productive maintenance (TPM) – Implementing key performance indicators – Guide. This new standard provides a consistently correct and effective approach to adopting TPM.
Maximizing efficiency
PAS 1918:2022 gives guidance on the concept of total productive maintenance (TPM) and on the key performance indicators (KPIs) that are relevant to implementing it. Guidance is provided on TPM for manufacturing plants and equipment. The aim of the PAS is to tackle the misapplication of TPM head-on, and help organizations adopt it correctly.
PAS 1918 sets out the basics of TPM as described in IATF 16949 for companies seeking IATF (International Automotive Task Force) certification. It does not preclude the expansion of the scope of application or the introduction of new technologies based on these basics.
The PAS also gives clear guidance on the implementation of TPM KPIs by any manufacturing organization in any region. This should lead to a consistent and standardized approach to TPM.
Correctly applied, TPM can help manufacturing and process industries to improve their productivity, increase their process efficiency and strengthen their risk management. It can enable organizations to find new customers and participate in new supply chains. Whether a manufacturing business wants to implement TPM for the first time or to make an existing implementation more effective, PAS 1918 can now supply authoritative guidance that ensures you get TPM right.