Author: Dr Seyed Ghaffar, PhD, CEng, MICE, MICT, FHEA
The UK is experiencing a housing crisis and the yearly number of homes being built is just half of what is needed, i.e. 300,000, to meet demand. Modern methods of construction (MMC) and manufacturing methods that harness digital techniques, e.g. RFID-BIM, have been encouraged as solutions to the industry challenges, with a particular emphasis on the potential of off-site manufacturing for residential housing. Modular construction in Europe and the USA could deliver annual savings of up to $22 billion[1].
Offsite construction is the manufacturing of the entire building block and assembly of components off-site in a factory, transportation and final installation at a chosen site. The term 'prefabrication', 'modular housing' or 'volumetric construction' are generally used more for in one-piece products, including manufacturing of structural volumetric spaces (e.g., enclosed modules or entire houses), non-structural volumetric spaces (e.g., bathroom pods), and wall panels (see figure 1). Finding the ideal combination of 2D panels, 3D modules and hybrid designs is necessary, as is addressing difficulties in design, production, technology, logistics and assembly. A comprehensive spectrum of "Modern methods of construction" utilised in offsite housing construction may be better understood with regularised terminology thanks to the MMC seven category definition framework. The DLUHC Joint Industry Working Group on MMC, responsible for enhancing stakeholder understanding of MMC, produced this defining framework [1].
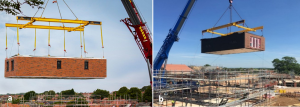
Figure 1 – a) The first of 131 off-site manufactured affordable homes have been installed in Arnold Nottinghamshire[2], b) ilke Homes installs first factory-built homes for Stonewater in Hereford[3].
A 2019 report published by the consultancy group McKinsey & Company found that offsite construction reduces timeframes for housing delivery, increases building quality, reduces waste and requires fewer trades on-site leading to overall cost savings compared to traditional construction methods [4]. Offsite construction can also lead to superior insulation performance due to factory precision, which in turn lowers household energy requirements and increases occupant comfort. Moreover, offsite construction is well aligned with the sustainable development of an urban environment by improving waste management and reducing on-site work and community disruptions.
With designing for deconstruction strategies in place, MMC makes it easier to reuse and recycle products at the end of a building's lifecycle. This could be a credible pathway to circular construction, an integrated management of construction and demolition waste [5]. Some builders are putting more emphasis on sustainability, aesthetics, and the higher end of the market in an effort to dispel the outdated perception of offsite housing, previously known as prefabricated housing as an unattractive, cheap, low-quality alternative. Just 7.5% of the homes built in the UK between 2017 and 2018 utilised MMC. While this percentage has increased annually, it is still far below the market leader, Sweden, with its enormous 45% [6].
The adoption of offsite construction methods are being pushed through a number of factors, including an abrupt increase in demand driven by customer preference for new homes and governmental support for offsite construction. It is also worth noting that unbalanced housing supply and demand have made it more difficult for vulnerable groups to afford a house, which has increased the need for government-funded initiatives to support housing supply. With its advantages, MMC can increase the supply of housing. Improvements in construction efficiency, cost, safety, sustainability, productivity, and quality are critical for achieving affordable housing and shortening the waiting periods for low-income groups. The speed of delivery of offsite construction can also be beneficial for the government to provide emergency shelters and other emergency response programs to meet sudden demand spikes such as disaster relief camps and for refuge seekers.
Offsite housing construction has been promoted as a radical innovative strategy to enhance the efficiency, quality and environmental performance of house construction. For example, research from Hong Kong shows a 52% reduction in waste generation across all building types, with the application of prefabrication [7]. Similarly, a thorough investigation of high-rise residential buildings in the UK revealed that MMC reduced overall construction time by 50%, waste by 70%, and led to an average cost savings of 30% compared to traditional techniques [8]. In addition, a study on the embodied carbon energy analysis of modern methods of construction in housing [9] found that a house constructed using an off-site panellised timber frame led to a 34% reduction in embodied carbon compared to the traditional masonry construction of the same house. However, the elimination of bricks and mortar, and its substitution with lower embodied carbon material, e.g., softwood timber, in the wall component was the main factor in the difference found. It is too simplistic, to consider embodied carbon as an isolated issue that can be resolved through offsite method of construction.
Offsite housing construction is an important radical solution which requires government policy development and demand stimulation, along with undertaking multi-residential demonstration projects to further evidence the potential of MMC. The huge investment needed to implement the concept of MMC acts as a barrier to their wider adoption. The lack of a demand pipeline that is sufficiently big and consistent to allow the market absorption of new houses and to sustain the financial viability of offsite housing construction is a major barrier impeding the transition to new business models for the delivery of housing. Moreover, the risks arising due to lack of standardised requirements for warranty and assurance entities is causing issues where the insurance and lending providers do not have the same confidence to open up finance for prefabricated housing construction, as they would for traditional build market. Additional financial commitments in the form of government grants, tax breaks, and subsidies should support offsite housing construction and planning policy incentives, such as fast-tracking of planning permission for offsite housing development may make it easier to implement this technology.
It is difficult to fully realise the economic and efficiency potential of MMC as it requires different skills than those employed in regular construction, which further hinders its adoption. The CITB has invested £1.2 million in educational resources for both classroom-based and hands-on training to up skill the workforce and improve the UK's capacity for offsite housing construction, which is a step towards improving the skills gap in the country [10]. Developing new design and manufacturing methodologies is also necessary, as is finding robust solutions to issues such as logistics and assembly.