
So you’ve spent hundreds of man hours, a chunk of money developing your brand new smoke alarm product, and now you need it certified. This may seem like a daunting process if you haven’t been through it before, but it need not be. Here’s our guide to product testing and certification – designed specifically to help you to navigate the process.
The Product Certification Process Explained
The first thing we need to know is the easiest - a full description of the product as you’d like it to appear on your final certificate. The key here is to use a description which conforms to the terminology of the standard, such as Mains Powered Photoelectric Smoke Alarm with Interconnect, Alarm Silence Feature and Battery Back-up.
A full description of the product provides us with 2 key pieces of information:
- How you would like the product to appear on your certificate upon the successful completion of the certification process
- The features that the smoke alarm provides which will be included within the specified test programme.
The second thing required is a full technical description or specification of the product. This can be provided in the form of the User Manual or some other document like a technical data or technical specification sheet containing the appropriate technical detail. The key here is that the document describes all of the functions / features that the product provides, whether optional or not.
So now you have provided the required information, what happens?
The next step is for the Certification Manager to review the information and design a programme of tests which will satisfy the requirements for product certification. Once completed the cost of the test programme along with certification costs such as application, factory assessment and certificate issue fees are sent to the applicant client in the form of a formal quotation.
Along with the associated costs, the quotation specifies the samples required for testing the lead time to testing and the testing turnaround times. These are the times between the receipt of the test specimens in BSI stores, to test commencement and the length of time required to complete testing (assuming no breaks in the test programme due to product non-compliance / failure).
Please refer to the following summary and if you have any questions, then please feel free to contact product.certification@bsigroup.com who would be pleased to explain the application process and answer any questions you may have.
Product Testing and Certification Sum
mary
Application
Application for Kitemark™ product certification is made using ‘Product Information Sheets’ and application for type test of the specific product.
The completed ‘Product Information’ Sheet is submitted along with supporting product information such as Technical Data Sheet, User Manual and/or Product Specification Information.
If application is being made for a series or a range of devices, then a detailed description of the similarities / differences between each device model in the series or range should be provided to help produce a more accurate test programme.
Application Acceptance
The completed ‘Product Information’ Sheet and supporting technical information is reviewed for completeness and to ensure that BSI can provide the services for which application is being made. This forms an important part of the contract review process.
At this stage further technical information such as circuit diagrams or PCB Layout Drawings may be requested. This allows an accurate schedule of tests and quotation to be produced and sent to you for acceptance.
Assessment
Quality Management System – BSI performs a third party independent assessment of the quality management system of the manufacturing facility to requirements of ISO 9001 and the product quality plan.
This ensures that the quality management system employed by the manufacturing facility produces product, which will be of a consistent quality and in compliance with the relevant product type test standard for which Kitemark certification is required.
The manufacturer produces corrective actions to any non-compliance’s raised during assessment of the factory quality management system.
Following satisfactory completion of quality management system assessment, a recommendation for quality certification is made.
If you have an existing registered quality management system with another accredited certification body, then BSI only need perform a production line assessment.
The assessment is performed against your production line quality plan and is specific to the product for which the Kitemark required.
Product Type Testing – BSI performs a third party independent assessment of the product in accordance with the requirements of the product type test standard and the requirements of a schedule of tests.
The manufacturer modifies the product to address any failures that occur during testing and re-submits the product for re-test and continuation of the test programme. Upon satisfactory completion of testing a test report is produced and reviewed by product certification for acceptance and inclusion in the product technical file.
Review
The test report is reviewed for accuracy against both the requirements of the product type test standard and the requirements of the schedule of tests.
One copy of the test report is held by product certification in the Kitemark technical file for the product and a copy is sent to the manufacturer.
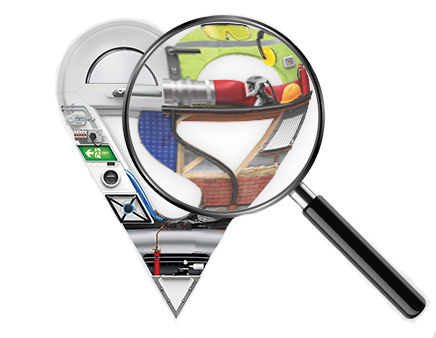
Kitemark
Once the test report has been sent to the manufacturer, the technical file is reviewed and closed. The Head of Product Certification then signs the Kitemark certificate, which is sent to the manufacturer granting use of the prestigious Kitemark in conjunction with the product marking.
Maintenance of your Kitemark Certificate
Continuing Assessment Visits (CAV’s)
Quality Management System surveillance visits are conducted at the manufacturing facility to ensure the continuing compliance of the quality management system with the requirements of the assessment standard (e.g. ISO 9001).
Where possible, the product audit sample is selected from stock or the end of a production line during the continuing assessment visit.
Product Audits – production representative sample(s) are audit tested at BSI premises, to ensure continuing compliance with the requirements of the product type test standard.
Conclusion
Undertaking Product Certification can be a difficult and complicated, but this depends on the point during the product development cycle certification is considered. If the product is designed with the product testing and certification requirements in mind, then the whole process is simpler and more cost effective. It is always good to bear in mind that product certification is necessary to separate compliant products from substandard.
At BSI, we’re able to offer direct pre-assessment testing and laboratory hire to help you during your product development process, leading the way to a smoother, more cost-effective certification process. Our team are available to help you every step of the way.
Contact us
For further information please contact:
Sales and Marketing
BSI
Maylands Avenue
Hemel Hempstead
Hertfordshire
HP2 4SQ
United Kingdom
Tel: +44 (0) 1442 278 607
Fax:+44 (0) 1442 278 630
e-mail: product.certification@bsigroup.com